Industrial imaging for optical sorting
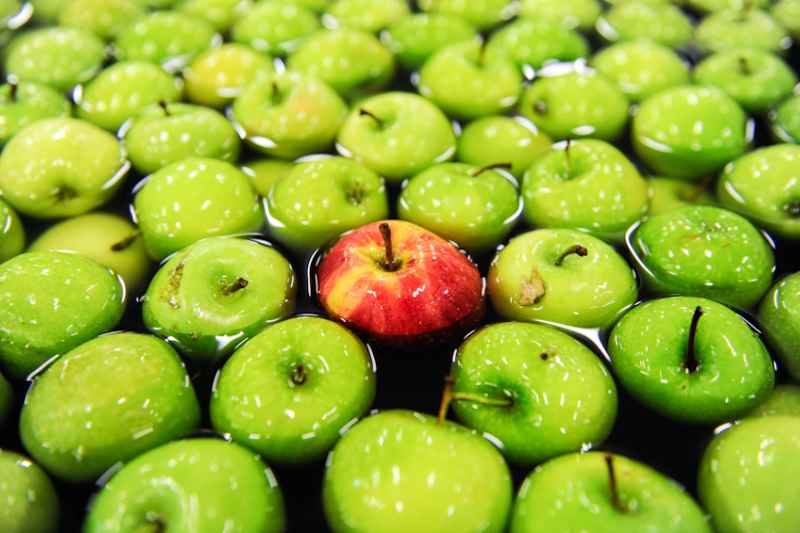
Optical sorting is the process of automatically sorting and separating different types of materials based on their optical properties, including color, size, shape and texture. It’s being deployed in more industrial applications to reduce labor costs and fatigue, and improve accuracy and efficiency. Common use of optical sorting can be found in the food and beverage industry, recycling facilities and mining operations, for example.
The implementation of optical sorting involves the use of sensors, precise lighting and high-speed cameras along with the analysis of the resulting images and data. Properties of the materials are determined so action can be taken based on pre-set criteria. This allows the sorting and grading of items, plus the rejection of faulty or flawed goods.
Technology for optical sorting systems
High-speed high-resolution cameras are a crucial component in optical sorting systems for accurate detection and identification of objects. They are usually mounted above a conveyor belt, and multiple cameras may be used to capture images from different angles. Autofocus-zoom cameras can enhance optical sorting, particularly in applications where a wide range of object sizes and shapes need to be sorted. The feature of automatically being able to adjust focus and zoom settings based on the size and position of the objects being examined enables very high-quality images of items passing through the sorting system, even at high speed.
Autofocus-zoom cameras with a global shutter, such as our Harrier 36x AF-Zoom IP Camera, are ideal for sorting applications as they can reduce blurring of fast-moving objects when compared to cameras with a rolling shutter. Furthermore, the IP capability of this camera means it can be added simply and quickly to a network where images from multiple cameras can be seamlessly processed and analyzed. While they may be a more expensive option than other machine vision cameras, the benefits in terms of image quality and real-time analysis may outweigh the initial investment cost, particularly in larger or more complex sorting systems.
An alternative to autofocus-zoom cameras would be to use a CoaXPress or Camera Link camera connected to a frame grabber. Camera Link is a robust and reliable interface, making it well-suited for the harsh conditions often encountered in sorting applications, such as refrigerated or cooled environments. The interface is designed to withstand temperature fluctuations, humidity, and vibration, ensuring reliable performance even in challenging conditions. Combined with one of our Camera Link frame grabbers, a sorting system will benefit from high-resolution, real-time image acquisition plus flexible triggering options. Additionally, Camera Link is a widely adopted interface in the machine vision industry, meaning that there are many supporting components available to choose from. This allows for greater flexibility in selecting cameras that meet the specific needs of the sorting application, such as camera resolution, frame rate, and sensitivity.
Like Camera Link, CoaXPress provides high data transfer rates, enabling very fast image capture and processing. CoaXPress can support data transfer rates of up to 6.25 Gbps per cable, and our FireBird Quad CXP-12 3PE8 supports up to four cables used in parallel to achieve data rates up to 50 Gbps. A further advantage of CoaXPress is its ability to support Power over Coax (PoC) technology. This allows power to be supplied to the camera over the same coaxial cables used for data transfer, reducing the need for more cables and simplifying installation. CoaXPress frame grabbers can also support multiple cameras in a single system, enabling the capture of multiple images from different angles or perspectives, providing more comprehensive data for sorting and analysis.
Imaging techniques for optical sorting
3D imaging allows for more accurate and detailed analysis of objects, as it captures a three-dimensional image of the materials passing through the sorter. This technology is particularly useful for sorting irregularly shaped objects that may be difficult to identify using traditional 2D imaging.
While there are several methods of capturing 3D image data, the most commonly used techniques in industrial imaging are:
Laser triangulation: this method uses a laser light source and a camera to measure the distance and height of an object based on the reflection of the laser light.
Time-of-flight (TOF) imaging: TOF imaging uses a laser light source and a camera to measure the time taken by the laser light to bounce back from the object. This measurement helps in determining the distance and position of the object.
Structured light: this uses a projected pattern of light onto the object, which is then captured by the camera. By analyzing the distortions in the projected pattern, the shape and size of the object can be determined.
Stereo vision: As the name suggests, stereo vision uses two cameras, similar to the way in which human eyes work, but relies heavily on algorithms which can solve correspondence issues between the two cameras.
Hyperspectral imaging is becoming increasingly important in optical sorting and industrial imaging. Using both visible and non-visible light, hyperspectral imaging enables identification of materials, and features such as the water content of an item. This means a sorting system can differentiate between items based on their chemical composition, so, for example, different types of plastic can be separated for appropriate recycling, and fruit can be examined for ripeness.
Applications benefitting from optical sorting
Optical sorters are becoming more widely used in agriculture and food processing to sort fruits and vegetables based on their size, color and shape. This allows for more efficient processing and packaging of produce, and also to identify and remove damaged or diseased produce, improving safety and quality in the food chain.
In the recycling industry, optical sorters are used to separate different types of materials such as paper, plastic and glass. This is important because different materials require different processing methods, and sorting them manually can be time-consuming and expensive. Using advanced imaging techniques enables more efficient and accurate separation of materials, resulting in reduced costs and increased recycling rates.
Optical sorters are also used in the mining industry to sort minerals based on their size, shape, and density. This allows for more efficient extraction of minerals and reduces the amount of waste generated in the process.
Sorting in this way can also be used to classify pharmaceutical products based on their color, size and chemical composition, helping to regulate the quality of medicines.
Integrating optical sorting
Our frame grabbers, cameras and embedded vision solutions are all suited to industrial imaging, and can be further customized as required. In the case of upgrading an existing system, or installing a new one, our team can advise on suitable vision components for industrial sorting systems, contact us to find out more.