New identity, same trusted name – but why?
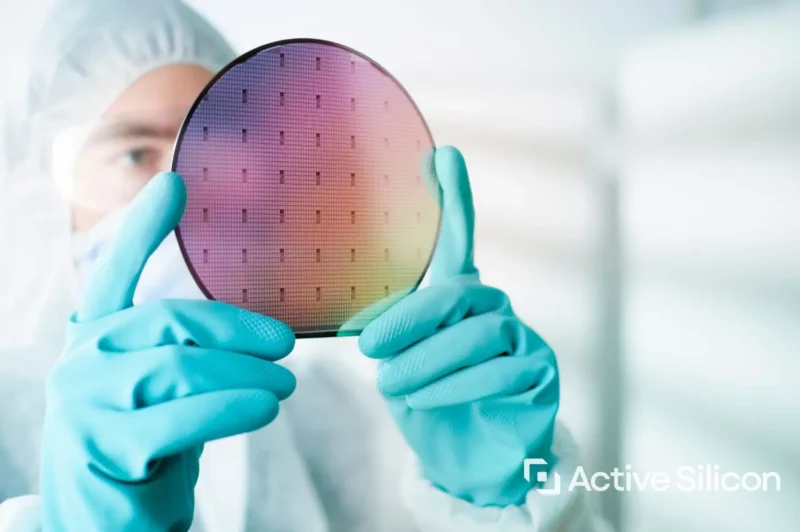
The name Active Silicon was decided in a discussion more than 35 years ago between company founders Colin Pearce and Chris Beynon. The use of “Silicon” made sense as our origins were in FPGA consultancy and is still relevant today as we expand our custom design skills beyond just imaging. “Active” not only placed us at the forefront of alphabetical lists but also at the forefront of proactive thinking and dynamic product development.
So we think it is a great choice of name honouring our roots and staying relevant through our company’s journey. Our fresh new logo ties in with our parent group’s branding as we sit alongside sister companies Steatite, Custom Power and Solsta, and expresses the unity and opportunity that the group as a whole offers.
To celebrate our ingenious name in combination with our new look, we wanted to share more about the use of “active” silicon in our work and related projects.
Silicon in cutting-edge photonics
In photonics applications, silicon is doped with specific elements to create optically active regions. This allows silicon to interact with photons, the fundamental particles of light, and perform functions such as absorption, emission, modulation, or detection of light signals.
One key application is silicon photonics, where silicon-based materials are used to manipulate light signals on silicon chips. Silicon photonics has grown in significance in recent times due to its potential for enabling high-speed data communication and processing with low power consumption, particularly in applications such as telecommunications, data centers, and sensing technologies.
Creating the optimum imaging components
Silicon also plays a crucial role in imaging technology, enabling the conversion of optical information into electrical signals, which can then be processed, manipulated, and stored to form digital images.
Complementary Metal-Oxide-Semiconductor (CMOS) image sensors are widely used in digital cameras, smartphones, and many other imaging devices. These sensors consist of an array of pixels, each containing a photosensitive element made of silicon. When light strikes these pixels, it generates electron-hole pairs within the silicon, creating an electrical signal proportional to the incident light intensity. This signal is then read out and processed to form a digital image.
All of our Harrier Autofocus-Zoom Cameras use CMOS sensors, ranging in size from 1/1.8 to 1/3 and in resolution from 2.5MP to 8MP.
Charge-Coupled Device (CCD) image sensors also use silicon. In a CCD sensor, photons of light generate charge carriers within the silicon, which are then transferred across the sensor’s array through a series of electrodes. This charge transfer process allows the sensor to capture and store the image information before it’s read out and processed.
And, of course, silicon is a core component in our FireBird frame grabbers, supporting the capture, processing, and transmission of video signals and for signal processing tasks such as color correction, noise reduction, image enhancement, and compression.
Control and configuration tasks within frame grabbers also rely on silicon to allow users to adjust settings such as resolution, frame rate, exposure, and gain. Microcontrollers, programmable logic devices, and communication interfaces enable users to interact with the frame grabber and customize its operation according to their specific requirements.
Silicon enables pioneering computer imaging
Very much at the forefront of computer technology, quantum concepts are regularly making headline news. Silicon-based qubits are being developed for their potential to create scalable and practical quantum computing systems with unprecedented computational power. For example, researchers at the University of Manchester, UK and the University of Melbourne, Australia, have been working on an enhanced, ultra-pure form of silicon that allows construction of high-performance qubit devices.
CERN, the European Organization for Nuclear Research, is using silicon extensively in its dedicated heavy-ion physics experiment, ALICE. The current Inner Tracking System is currently the world’s largest pixel detector with 10sq.m. of active silicon area and nearly 13 billion pixels. The team are developing a new Inner Tracking System (ITS3) which will enhance the experiment’s capabilities even further. Alex Kluge and Magnus Mager, the project leaders of ITS3, commented that “ALICE is like a high-resolution camera, capturing intricate details of particle interactions. ITS3 is all set to boost the pointing resolution of the tracks by a factor of 2 compared to the current ITS detector.”
Keeping silicon active
Our innovative designers will be continuing to push silicon to its limits in our cutting-edge imaging products, keep an eye on our social channels to be the first to hear about new developments.