Automated Vehicles for Robotic Inspection: The Role of Computer Vision in ROVs and UAVs
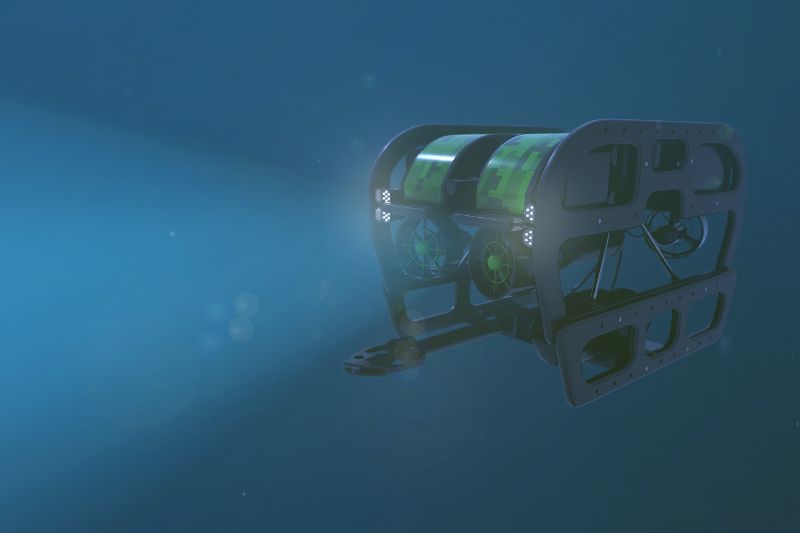
The industrial landscape is undergoing a significant transformation with the emergence of automated vehicles equipped with computer vision and advanced software. Remotely operated vehicles (ROVs) and unmanned aerial vehicles (UAVs) are revolutionizing inspection operations in various sectors, from energy to agriculture and beyond. We’ve looked at the impact of autonomous vehicles on robotic inspection, with a focus on how computer vision is enabling these vehicles to perform tasks more efficiently and safely.
Offshore Oil and Gas Applications
The offshore oil and gas industry has relied on traditional drones operated by experienced pilots. However, the rise of autonomous drones has brought about a paradigm shift in this sector. These autonomous vehicles are equipped with advanced computer vision systems and collision avoidance software that enable them to operate in challenging environments with ease. They can adapt to changing weather conditions and navigate obstacles, making them more reliable and safer for inspection missions than previous options.
One notable advancement in this field is the introduction of drone docking stations. Companies like Energy Robotics offer solutions such as the “Drone-in-a-Box,” which allows for fully automated missions. These docking stations enable drones to take off, perform inspections, and return to their base autonomously. This technology not only reduces the need for human intervention but also enhances the efficiency and reliability of inspections in the offshore industry.
Autonomous Ground Robots for Industrial Inspection
In addition to UAVs, autonomous ground robots are becoming increasingly popular for inspections on rigs and energy facilities. Quadraped robots, manufactured by several companies, can navigate various terrains, including slopes and steps. These robots are equipped with a range of sensors, including vision, sound, temperature and gas leakage detectors to enhance their inspection capabilities. Ghost Robotics demonstrated the functionality of their VISION 60 robot on our stand at the DSEI show recently, controlled by an MPU5 radio available from our sister company, Steatite.
High-resolution cameras are a fundamental component of these autonomous ground robots. These cameras provide crucial visual information that allows the robots to navigate and perform inspections effectively, which may be required in real-time by a remote operator. Many of these robots are also designed to operate in hazardous environments and are certified to meet safety standards and directives such as ATEX.
Underwater ROVs for marine inspection
Subsea imaging has developed greatly over the last decade or so to provide a valuable option for underwater rig, pipeline and vessel inspection. Autonomous underwater vehicles (AUVs) greatly reduce operational cost and increase safety aspects as they eliminate the need for specialized dive teams to carry out maintenance checks. These vehicles are also used for advanced scientific research, such as the Autosub Long Range autonomous vehicles owned by the National Oceanography Centre (NOC) in the UK and powered by battery packs from our sister company, Custom Power.
Digital Twins
The integration of digital twin technology in industrial applications has enabled the training of artificial intelligence (AI) and the development of automated maintenance programs. Digital twins create virtual replicas of physical assets, allowing AI systems to simulate and learn from real-world scenarios. This technology plays a pivotal role in improving the efficiency and effectiveness of autonomous vehicles in industrial settings as simulated data can be used to train ROVs and UAVs.
Robotics as a Service
The concept of “robotics as a service” (RaaS) is gaining traction in the industry. Instead of investing in and maintaining their fleet of autonomous vehicles, companies can now hire these vehicles and skilled operators from dedicated contractors. This outsourcing model allows businesses to focus on their core operations while leveraging the expertise of contractors for inspection missions that require specialized knowledge and equipment. The service is usually subscription-based, making costs predictable and allowing end-users to benefit from developments in technology without the associated R&D costs.
Environmental Impact
The adoption of autonomous inspection vehicles is not only about efficiency but also environmental sustainability. By reducing the need to transport teams of people to and from inspection sites, these vehicles significantly reduce the carbon footprint associated with industrial operations. This aligns with the growing emphasis on environmental responsibility and sustainability in today’s world.
Predictive Maintenance
Furthermore, ROVs and UAVs equipped with AI capabilities play a crucial role in predictive maintenance. Beyond capturing images of machinery, these AI-driven vehicles can make informed decisions about whether maintenance or repairs are necessary. This proactive approach to maintenance can help prevent costly equipment failures and downtime, further enhancing efficiency and safety in industrial settings.
Overcoming Challenges in Remote Inspection
One of the challenges in remote inspection using drones and ROVs is network connectivity. Operating in remote or offshore locations can pose difficulties in maintaining a stable and high-speed data connection. Additionally, ensuring the security of the data being transmitted is paramount.
To address these challenges, industries are investing in robust network infrastructure and implementing advanced IT security measures. These measures are essential to ensure that data collected by autonomous vehicles is transmitted securely and efficiently to remote locations for analysis and decision-making. A mobile ad-hoc network (MANET), such as is used by the MPU5 radio, can be created to overcome environmental, geographical and logistical challenges, read about this incredibly versatile technology.
Imaging Techniques used in Robotic Inspection
High-Resolution Photography and Videography: High-resolution cameras are the workhorses of autonomous vehicles in industrial settings. These cameras capture detailed images and videos, which are essential for a wide range of applications. For example, in offshore oil and gas inspections, high-resolution imagery can help identify corrosion, structural damage, or other anomalies in equipment and infrastructure. In the context of energy facilities, detailed imagery can be used for asset tracking, security monitoring, and maintenance planning.
Our range of Harrier AF-Zoom cameras offers Full HD and 4K cameras, available with a variety of outputs including Ethernet and wireless IP, HMDI, USB 3 and and with zoom options up to 55x.
Thermal Imaging: Thermal cameras capture infrared radiation from objects and can provide valuable information about temperature variations. In industrial inspections, thermal imaging is used to identify hotspots, energy leaks, and potential equipment failures due to overheating. For instance, a UAV equipped with thermal cameras can detect heat anomalies in electrical systems, pipelines, and machinery, helping prevent fires or equipment breakdowns.
Multispectral and Hyperspectral Imaging: Multispectral and hyperspectral cameras capture data across a range of spectral bands, including visible and non-visible wavelengths. These cameras are used in agriculture, environmental monitoring, and geological surveys. In agriculture, for instance, multispectral cameras on UAVs can detect variations in crop health by analyzing reflected light in different spectral bands, enabling precision farming practices. Check out Tevel’s agricultural robot, autonomously inspecting, selecting and picking fruit in orchards and fields across the globe.
LiDAR (Light Detection and Ranging): LiDAR sensors emit laser beams and measure the time it takes for them to bounce back, creating highly accurate 3D maps of the environment. LiDAR-equipped vehicles, including ground-based robots and UAVs, are used in industries like construction, mining, and forestry. They can create detailed terrain models, monitor stockpile volumes, and aid in autonomous navigation by providing a rich 3D environment representation.
Underwater Sonar Imaging: ROVs specifically designed for underwater applications often use sonar imaging in addition to traditional cameras. Sonar systems use sound waves to create detailed images of underwater structures, shipwrecks, or subsea pipelines. This technology is crucial for offshore inspections, underwater archaeology, and marine research.
3D Scanning and Photogrammetry: These techniques involve capturing a series of images from different angles and then processing them to create 3D models. In industrial contexts, 3D scanning and photogrammetry can be used for asset documentation, quality control, and building digital twins. For instance, an autonomous ground robot equipped with cameras can create precise 3D models of a facility’s interior for planning and maintenance purposes.
Machine Learning for Image Analysis: In many cases, the images and data collected by autonomous vehicles need to be processed and analyzed in real-time or later for decision-making. Machine learning software tools, including object detection, classification and segmentation, are employed to extract valuable insights from images and videos. For example, object detection algorithms can identify and track specific components or anomalies in industrial equipment, enhancing predictive maintenance efforts.
Augmented Reality (AR): AR is another software tool which is used to overlay digital information, such as schematics, maintenance instructions, or real-time sensor data, onto the live video feed from autonomous vehicles. This enhances the situational awareness of operators and technicians, aiding in complex tasks like equipment maintenance and repairs.
The rise of automated vehicles in robotic inspection, particularly in the form of ROVs and UAVs, has ushered in a new era of efficiency, safety and sustainability. Computer vision technology is at the core of this transformation, enabling these vehicles to navigate complex environments, collect valuable data, and contribute to predictive maintenance efforts. As industries continue to embrace autonomous vehicles and the advantages they bring, the future holds the promise of even greater innovation and optimization in the industrial landscape. The integration of AI, digital twins, and robotics as a service will play a pivotal role in shaping the future of industrial applications.
At Active Silicon, we pride ourselves in remaining at the forefront of imaging innovations and continue to invest in R&D to deliver advanced computer vision products for cutting-edge industrial and inspection tasks. Contact us to see how our expertise can help your autonomous vehicle deliver real value to your business.