Selecting a camera for your machine vision application
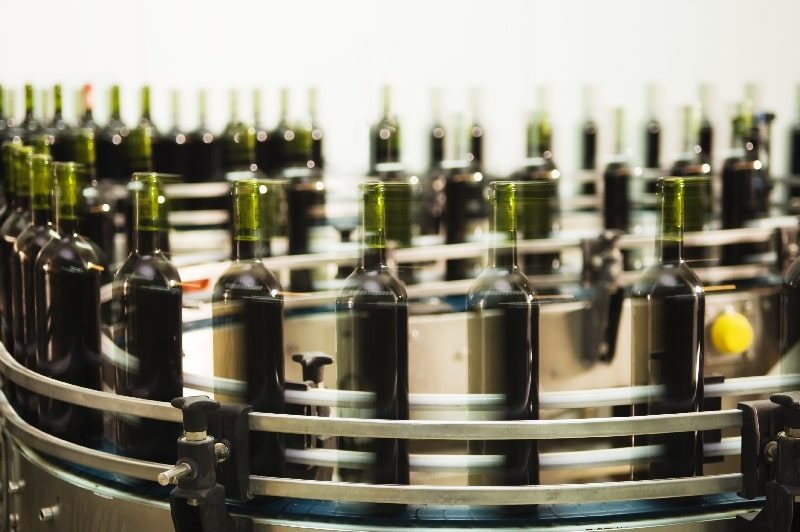
Today’s market offers a plethora of innovative machine vision cameras, but what do you need to know when selecting hardware for your application? We’ve compiled some brief pointers.
2D cameras are by far the most widely used and perform very well when consistently-shaped parts are presented to vision sensors on a flat surface. CCD sensors have been overtaken in popularity by CMOS sensors, as these have become less expensive, offer high resolution and are able to keep up with advancements in line with Moore’s Law. Example applications are industrial inspection in a controlled environment, such as checking for foreign objects on a production line.
3D cameras capture a perception of depth. Although today’s 3D cameras are still relatively bulky, they are offering new options in picking and placing for industrial robots. Time of Flight (ToF) cameras have become increasingly more affordable over the past five years or so and offer an inexpensive method of 3D imaging. They work by measuring the time it takes for infrared light emitted by the camera to reach the subject and return, thereby calculating distance. Other 3D vision technologies include stereo vision and structured-light. Stereo vision uses two cameras, similar to the way in which human eyes work, but relies heavily on algorithms which can solve correspondence issues between the two cameras. Structured-light involves projecting known patterns onto the object and reviewing the pattern distortion, a method which works well for static objects but is subject to blurring due to a low frame rate. 3D cameras are ideal for enhanced production line inspection where understanding volume and distance are needed, or for mobile applications requiring object avoidance.
Infrared cameras capture the IR rays emitted by the target object to calculate edges and absence/presence detection. They are excellent for differentiating between materials but operate best in low-light conditions, making them well-suited to, for example, leak detection.
Ultrasonic, or sonar, cameras measure sound waves rather than light, so can be effective regardless of lighting conditions. Sonar cameras are best used in dark, dusty or smoky environments but can be affected by interference from noise, humidity and pressure. Ideal applications are collision avoidance and measuring liquid levels.
Multispectral and hyperspectral cameras encompass sensors which can detect light across a broader spectrum than the human eye and interpret this into useful data. They are being widely introduced in medical imaging, to differentiate between different tissue types, and in agriculture, to monitor crop health and hydration levels. Wider use of ROVs and drones is leading to a larger market sector for these cameras. You can read more about the use of these cameras in our recent blog, “Applications for multispectral and hyperspectral imaging”.
Area scan v line scan cameras. JAI has compiled an excellent white paper on the different benefits of color line scan and area scan cameras. This is well worth a read to understand which option will work best for your application, and also gives a very interesting overview of Bayer, prism and trilinear camera technologies. As outlined in the paper, area scan cameras are a good choice for inspecting items which have clear boundaries and are presented uniformly. However, line scan cameras offer resolutions far greater than those of area scan and are ideal for moving objects such as those on a conveyor belt.
Selecting the right camera was just one aspect of HD video transmission that our Head of Sales and Marketing, Frans Vermeulen, touched on in his presentation at the UKIVA Machine Vision Conference last week. Contact us to understand more about how our expertise and market-leading hardware could improve your industrial application.