Active Silicon’s AI Series – part 5: AI and computer vision are bringing Industry 4.0 to a smart factory near you
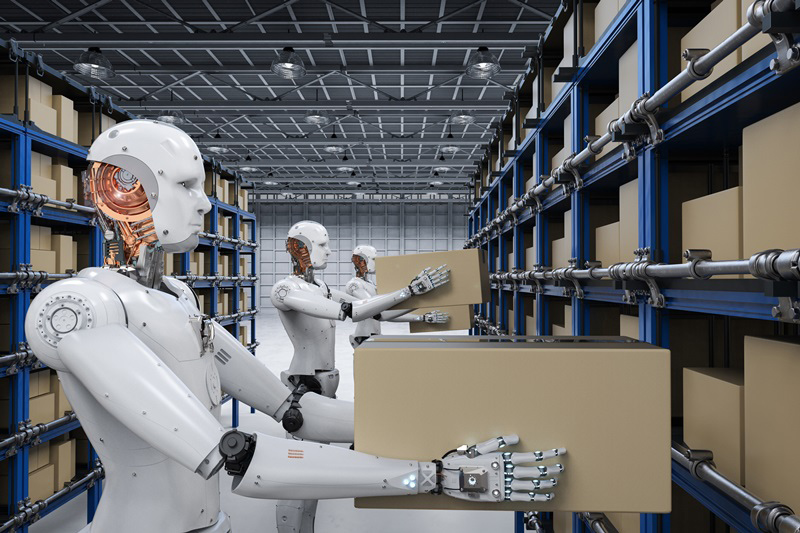
Our recent blog Industry 4.0: what does it mean for machine vision? covered the impact that the 4th Industrial Revolution is having on our sector. A major factor in the development of the so-called revolution is the adoption of Artificial Intelligence (AI) software allowing machines to learn and process information to a better degree than humans. So, what influence is AI having on modern developments? Three principal areas form the focus of current discussions: automated quality inspection, predictive maintenance and the role of robots.
Quality inspection
Several organizations are claiming to offer the first software suites to bring deep learning to machine vision, for example Vidi from Cognex in the industrial imaging sector. They are being closely followed by companies who are adding machine learning capabilities to their portfolio, such as Cyth System’s Neural Vision and Sualab’s Vision Inspection AI solutions for textiles, leather and printing inspection. But how do they work?
Instead of the traditional method of inspection, where vision systems use cross-correlation or pattern matching to check for anomalous shapes, fill levels, irregular sizes and foreign bodies, AI inspired algorithms and Artificial Neural Network systems can now be used to teach computers to evaluate the quality of a product in the same way that a person can – for example, to look for an unacceptable level of imperfections on the skin of a fruit, or too many flaws in a textile roll. These processes are no longer required to be limited to “pass” or “fail” results, but can allow greater classification of products, and even select defective items for correction where deemed possible. As you would expect, these computers can work faster than a human workforce, and without rest, allowing manufacturers to increase their yield massively. It is even possible, as a result, for production processes to be automatically reviewed and enhanced to prevent recurring faults.
The game changer here is not the level of AI software being made available, but the level of expertise required to implement the new software. Cyth claim that Neural Vision can be implemented by a programmer with no machine vision experience whatsoever, and MVTec’s well established HALCON library promises a new release which will allow users to train CNNs themselves, thereby potentially increasing the number of applications incorporating AI into their inspection systems.
Predictive maintenance
The practice of monitoring and repairing faults and wear in machinery before they cause a breakdown or stoppage of the production line is being made faster and more efficient using machine vision and AI software. Data and images of machinery, robotics, belts and cables captured by sensors and cameras can be recorded and processed using algorithms programmed to trigger an alert when intervention is necessary. Developments in big data and cloud computing mean that a vast amount of data can now be handled over an enormous geographical range, allowing production managers based in one continent to repair and replace production line equipment in another. Additionally, new technologies allowing more data processing to be carried out near the processing unit (at the edge) rather than sending it to the cloud means that even more information can be handled and processed. Such programs also enable a more efficient servicing schedule for equipment, ensuring that maintenance is carried out as and when necessary, rather than simply because a machine might be due its annual check-up!
So, AI is changing factory floors at an unprecedented rate, bringing the Industry 4.0 revolution to even more production lines and inspection facilities. But at what cost to us humans?
The role of robots
We’ve all read about robots becoming smarter and more independent, even to the extent that world domination is feared by some. Without doubt, robots powered by AI have an important role to play in the Industry 4.0 revolution. Robots have been used in industrial settings for decades, carrying out simple, repetitive tasks on a production line, or moving items around a warehouse. Historically, they have had limited intelligence, and have had to work separately to humans for fear of injury. That’s all changing. As an example, Rethink Robotics has spent the last five years developing collaborative robots (cobots) for use in industrial settings. In 2017, Alicona released Tool Cobot – a fully portable industrial collaborative robot which brings 3D optical metrology to the next level. Using machine vision and smart technology, these robots operate alongside workforces, keeping production efficient, and their human colleagues safe. We can see such another use case with Ocado’s Smart Platform robots, which bring goods in the warehouse to the human picker instead of the picker spending time walking to the goods[1]. Now AI promises to make robots even more autonomous and cerebral as they begin to think and act like humans. This, of course, is great for production processes and bottom line reporting, but what’s the impact on real people?
Two opposing camps put forward arguments here – the first maintains that robots will replace people in many jobs, from picking in a warehouse to loading and driving a delivery truck, and unemployment will inevitably rise. Add to that the perceived threat of AI enabling machines to become too clever, and it might not just be our labor pool that robots are disrupting but our everyday lives and security too.
The other side states that robots will take only the most monotonous jobs, encouraging humans to train for more skilled roles, thereby creating an enhanced working environment. Furthermore, these advocates affirm that, as robots in the Far East cost about the same to implement and run as robots in the West, we could see a shift to local production instead of the east-bound outsourcing that we’ve seen in past years, electronics manufacturing being a prime example. The benefits of using a low-cost, Asian workforce will become outweighed by the savings created by automating and optimizing production lines in Europe and the US. Additionally, consider the shortened shipping time associated with local production, and the increasing demands by consumers for priority delivery at low cost could be better met.
The key word when looking at the human versus robot argument is collaboration: collaboration between man and machine; collaboration between internal company departments with different objectives; collaboration between organizations with different expertise. If these areas cooperate successfully, benefits to all can be maximized and threats minimized.
AI and machine vision is bringing Industry 4.0 to a factory near you
Whatever the eventual outcome, combining machine vision, AI and Industry 4.0 is promising to change the engineering world as we know it. Industry has a lot to learn from the smartphone manufacturers and consumer tech organizations who are developing miniature and embedded systems at a rate of knots; opportunities to implement advanced and intelligent systems to optimize production and inspection are extensive and exciting.
Read more from our AI Series here, or contact us to see how machine vision could improve your products and processes.
[1] http://www.connectivity4ir.co.uk/article/140893/Ocado-s-I4-0-solutions-make-packing-groceries-that-much-smarter.aspx?utm_source=emailmarketing&utm_medium=email&utm_campaign=20171130nl&utm_content=2017-12-01