Time to move on from Industry 4.0?
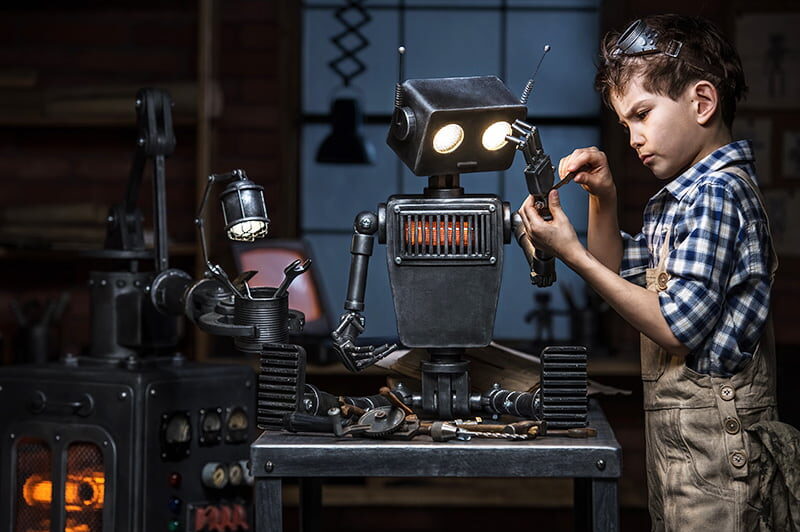
There’s a new kid on the block – Industry 5.0 is emerging. What’s this all about, and what’s actually different from Industry 4.0?
Industry 4.0, or the Industrial Internet of Things (IIoT), is now a pretty familiar term to most of us and it’s becoming widely established across the globe. In our previous news stories, you can read an introduction to Industry 4.0 and more about the associated technologies and processes.
The basics of Industry 4.0
Industry 4.0 has been all about making manufacturing smart. It’s meant adding numerous sensors to factory production lines to collect huge amounts of data, and learning to process, interpret and act on that data. Many mundane, repetitive and also dangerous human tasks have been replaced by robots and computers. Machine learning and AI have played their part in achieving high levels of automation throughout the industrial world.
Image processing also plays a key role in Industry 4.0. Capturing image data, processing this information, and instructing other devices is a fundamental part of creating and operating smart factories. Machines that can “see” are now being trained to use images to make decisions, speeding up and refining identification and inspection processes.
What does Industry 5.0 mean?
The Publications Office of the EU has described it as follows:
“Industry 5.0 complements the existing Industry 4.0 paradigm by highlighting research and innovation as drivers for a transition to a sustainable, human-centric and resilient European industry.[1]”
So are we bringing industry back to the people?
Not exactly. Industry 5.0 is another step in the journey to automation, but one where humans are recognized as essential and adding value. It was all too easy to get swept up in the IIoT wave and prepare for robots replacing our entire living workforce.
Industry 5.0 puts the brakes on that and reminds us that humans are needed for, firstly, their design abilities, problem solving and creative thinking and, secondly, the good of the planet. Also, all too complex automation processes can in some cases be counterproductive. An example of this was Tesla’s Model 3 production line, where Elon Musk was forced to come up with drastic measures to ensure that already lowered targets were met and resulting in his famous tweet, “excessive automation at Tesla was a mistake. To be precise, my mistake. Humans are underrated”.
Customization is key
In a world where advanced tech is at our fingertips and new products and innovations are surfacing daily, the ability to customize their offering gives companies a massive advantage in a competitive marketplace. And while AI is amazing, it’s really only as clever as the engineer that feeds it (albeit faster!) Bespoke, luxury and itemized products still benefit from the human touch.
Still a role for factory workers
Furthermore, people need jobs and, while some will embrace the IIoT dream of robots packing boxes on production lines, leaving the workforce to train into new and more varied and skilled roles, others will see the necessary re-training as a hurdle and the roles taken up by robots effectively a loss of jobs, especially for unskilled workers.
Industry 5.0 is really a utopia where humans and computers synergise and evolve together. But is Industry 5.0 an industrial revolution in its own right? Is it characterized by ground-breaking achievements like the preceding industrial revolutions, or is it rather the ultimate goal that we must strive for when implementing Industry 4.0? As the EU lays out, advancement in industry must be balanced with advancement in society. A world of collaboration is the goal.
The rise of the cobot
We’ve all heard about collaborative robots (cobots) and seen some amusing and awe-inspiring videos on social media (such as Universal Robot’s seemingly classically trained dancing cobot!). Industry 5.0 is about making these commonplace. The robots created in the rush of Industry 4.0 often need to work behind safety fences as they carry out dangerous tasks, such as welding or heavy lifting, separated from their human colleagues. Cobots break down these fences.
Technology companies such as ABB have been building and distributing highly flexible cobots for some time. An ABB survey confirmed that 85% of respondents “said the pandemic had been “game changing” for their business and industry, with COVID-19 a catalyst for accelerating investment in automation”[2]. Therefore, the latest addition to their portfolio, the GoFa™ and SWIFTI™ cobot families, are designed specifically to be intuitive enough for non-specialised staff to be able to implement and run. These out-of-the-box solutions bring automation to a wide range of smaller, less tech-savvy production lines.
Innovations in hardware are also being matched by innovations in software. Veo Robotics launched FreeMove® in 2021, their advanced safety system for industrial workcells with human-robot collaboration. This aims to enable safe interaction between humans and robots using 3D monitoring, tracking and calculating capability and a stop and restart function.
Industry 5.0 automation leaves the human workforce in the room – physically and metaphorically. Humans will be able to work alongside collaborative robots, which are built to assist rather than replace people. It’s being recognized that computers cannot run the industrial world alone and the value of human partnership is back on the boardroom table.
Up-skilling and re-skilling opportunities
In addition to the “blue-collar” and “white-collar” roles that we’re familiar with, Industry 5.0 is creating what’s being called “new-collar” workers – those who receive technical and soft-skills instruction in a work environment or vocational training rather than through a traditional education pathway. They include the database managers, cybersecurity experts and cloud computing engineers of the future. Specific skills being developed include CAD skills, data analytics, digital skills around additive manufacturing and, of course, understanding robotics.
Established robot manufacturer, FANUC, is leading by example here, having recently announced a partnership with Rockwell Automation to launch accelerated work and learn apprenticeship programs designed to upskill current and future workers for jobs in advanced manufacturing, robotics and automation. Successful recruits will be accredited with basic level qualifications (such as Robot Operator) right up to Integration Specialist level.
The future is 5.0
Industry 5.0 aims to change the shape of the industrial workforce, while maintaining its size and scope. It’s an exciting opportunity for us all to embrace a digital future and at Active Silicon we’re ready to meet the advanced requirements and customizations of modern manufacturing with our industry-leading vision products.
Stay up to date with more industry developments – we bring you the latest news in our blogs, or sign up to our newsletter.
[1] https://op.europa.eu/en/publication-detail/-/publication/468a892a-5097-11eb-b59f-01aa75ed71a1/
[2] https://new.abb.com/news/detail/74784/abb-launches-next-generation-cobots-to-unlock-automation-for-new-sectors-and-first-time-users