Autofocus-Zoom Cameras for ROV Applications
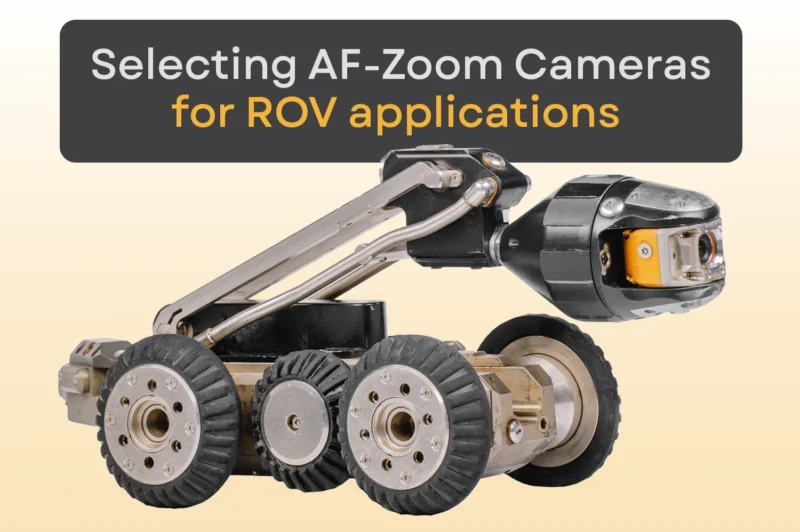
Camera selection for ROVs is an important and often complex process. Several factors influence which block camera will be optimal for the application in mind. This blog considers the options and aims to help guide engineers in making the right choice.
When it comes to remotely operated vehicles (ROVs), whether they are used for underwater surveillance, pipeline inspection, defense applications or industrial tasks, the camera is arguably one of the most critical components. It’s the primary sensor that provides the operator with real-time visual feedback and enables navigation and data collection. Among the various camera types available, autofocus-zoom cameras have gained significant traction due to their ability to provide flexible, high-quality imaging in dynamic environments. When selecting the right camera for an ROV, engineers must weigh a multitude of factors to ensure that the camera performs reliably under specific operational conditions.
Important Camera Considerations for Remote Inspection
Autofocus-zoom cameras stand out because they combine the ability to change focal lengths with automatic focus adjustments. This is particularly valuable in pipeline inspection, where visibility and object distances can vary. The ability to zoom in on structural flaws as the ROV moves through the pipe can mean the difference between capturing critical details and missing them altogether. However, this added complexity also introduces more technical variables that need to be considered.
One of the first decisions engineers must make is the level of zoom required. Optical zoom is preferable to digital zoom, as it maintains image quality throughout the zoom range. The right level depends on the ROV’s operational scope. For detailed assessments, such as pipeline inspection, a higher optical zoom range is advantageous. However, it is also important to balance zoom capability with camera size and weight, especially on smaller ROV platforms where payload limits are strict.
Another crucial aspect for inspection ROVs is how well the camera’s autofocus and automatic exposure (AE) system handles challenging lighting conditions. In environments with low contrast or poor lighting, some autofocus/AE systems may struggle. Engineers should look for sensors with good low-light sensitivity (e.g., larger CMOS sensors with high ISO capabilities), and cameras that support wide dynamic range (WDR) for handling areas of high contrast.
Video output options are another area where engineers need to make informed choices. The most common video outputs for ROV cameras are SDI, HDMI, and Ethernet IP. Each has its pros and cons. HD-SDI is often favored in inspection setups due to its ability to transmit uncompressed, low-latency HD video over long distances of coaxial cable – ideal for real-time control.
HDMI can provide excellent image quality but is expensive, less robust over long cable distances and not always suited for tethered systems.
IP cameras offer the advantage of digital control and easier integration into networked systems but they do come with the disadvantage of longer latency compared to the other two output formats. Latency is an important consideration especially for applications that require tight real-time control, you can read our technical note on reducing latency in IP cameras to understand how to optimize your IP system.
Latency in this context refers to both delays in video transmission and also the time it takes for the camera to zoom and re-focus. Autofocus and zoom functions should respond promptly to operator input, especially during precise maneuvering or close-up inspections. Cameras that introduce noticeable delay can hinder performance or even result in defects being missed entirely. It’s important to test camera systems in real-world conditions – or at least simulate them – before final deployment.
Physical durability and environmental resistance are non-negotiable for cameras being used in industrial inspection applications. Cameras should be housed in IP-rated enclosures appropriate for the environment. For underwater use, these housings also need to be pressure tolerant. For use in warmer environments the designer will have to consider how to keep the insides of the enclosure cool, this can be a limitation on the electronics used inside the ROV. System designers should also consider temperature ratings, corrosion resistance, and how easily the camera can be maintained or serviced in the field.
Finally, integration matters. An ideal autofocus-zoom camera will support remote control via industry-standard protocols such as VISCA or Pelco-D, allowing operators to control zoom and focus from remote locations. It should also be compatible with the ROV’s power supply and have a manageable interface for maintenance, software updates, and field calibration. Engineers should also consider whether the camera can be easily swapped out or upgraded, particularly in mission-critical or rapidly evolving operational environments.
Selecting a Block Camera for ROVs
Choosing the right block camera for an ROV involves a careful balance of technical features, environmental durability, and system integration. Engineers must consider zoom range, autofocus performance, video output format, low-light capability, and how well the camera integrates with the broader control and power systems. By evaluating these factors in the context of the ROV’s specific mission requirements, operators can ensure that the camera delivers reliable, high-quality video for maintenance and inspection operations.
Our range of Harrier Autofocus-Zoom Cameras includes options with 10x up to 55x zoom, various outputs such as 3G-SDI, HDMI and IP Ethernet, and global shutter or rolling shutter sensors. Several models are already deployed in ground and subsea ROVs, carrying out essential inspection and repair work. Take a look at the options or contact us to discuss a custom-designed solution.